Engineer Quality - Plant Job in Varroc Excellence
Engineer Quality - Plant
- Aurangabad, Bihar
- Not Disclosed
- Full-time
- Permanent
Job Description Quality Control & Improvement: Conduct RCA of recurring issues (internal/external customer), analyze & implement timely CAPA for fixing gaps to ensure no repeated issues. Handling Inspection messurment Like CMM,Profile projector,Roundness tester Etc. Skill for internal Calibration of Gauges and Instrment Ensure action plans from audits are implemented to close all the non-conformities. Ensure all laid out procedures and tests and QMS documentation are implemented as per VQS. Develop the Incoming Quality check plan with respect to sampling plan and at par with Customer specific requirements (for Raw materials, BOP etc.) Conduct rating process for suppliers on quality parameters & functional/fitment checking of parts to be dispatched. Ensure parts to be dispatched by plant are checked for rust, dust, dent, damage, mechanical parameters etc. and conduct final visual inspection. Prepare various reports (Audit, CAPA, Complaints etc.) independently. Analyze process to find improvements, analyse the root cause of any problem that occurred with CFT, and identify any non-value-added activities Choose statistical technique with optimum amount of data required to ensure adequate resources and due dates are met for test report writing, with supervision Quality Assurance: Communicate the importance of the implementation of QMS procedures to all units. Cascade the concerned procedures to the respective process owners (Engineering, Production, PPC, Logistics, etc.) Design, implement and document procedures for process control, process improvement, testing and inspection, with limited supervision. Define metrics for measuring performance on quality parameters in units. Develop procedures for end-to-end quality assurance from sample collection, analysis to disposal Conduct audits of manufacturing process parameters, Product & System and ensure deviations are corrected Recognize causes and consequences of quality issues that are not readily apparent while doing cause analysis. Identify gaps in information and predict/gather relevant data in order to continue analysis and/or initiate suitable corrective action Use GD8 principles / Customer Specific formats to solve issues in the plant related to Quality of process and Product. Ensure Lesson Learnt, PTDB for all the failure in-house & customer are updated timely to Design team for future reference to ensure No re-occurrence of issues. Quality Systems Application: Understand customer quality requirements (process and product characteristics) Be active member in CFT for development of Process documents during the Product Planning process (Gate 0) and all steps of DFMEA Participate as CFT member to Calculate the SOD (Severity x Occurrence x Detection) number or risk priority number (RPN) as part of PFMEA Develop robust Control Plans ensuring effective SOPs and WI (Work Instructions) at par with PFMEA. Quality Alignment with New Product Development: Support concurrent engineering efforts by participating in design & development projects representing quality assurance and the customer Be part of CFT with R&D, ME team to compile the DFMEA matrix taking inputs from all team members. Implement if there are no new technical inputs required In case of ECN, else coordinate with PM & TC for changes Collect PTDB (Past Trouble Database) i.e. TGW (Things gone wrong) of earlier projects and TGR and make team members aware of the same Customer Complaint Management: Ensure process fool proofing (Poke Yoke) - Detection & Occurrence Poke Yoke List the no. of Poke Yoke installed in Plant Conduct Poke Yoke Audit at defined frequency through rabbit test (NG Sample) & Negative Validation Ensure all deviations are approved by Plant quality Head supported by Plant Head Ensure 100% On time CAPA index, Replication, plan adherence, cascading for complaints involving machine operators closure of all complaints, submission of CAPA within stipulated time Quality Management System adherence: Communicate the importance of QMS procedures to all units, during roll out, implementation & updates Track changes in QMS implementation at plant and deal with issues if any Support the development and administration of the customer CAPA, internal non-conformance according to Varroc Quality Management System Utilize various tools to evaluate the effectiveness of the quality system including management reviews, internal audits, feedback from internal and external customers, warranty data, and traceability, etc. Monitor progress status against open issues of all audit engagements to ensure closure. Ensure retention of all customer documents as per CSR timelines Assist QMS Head in development of QMS procedures which are aligned with Customer specific requirements
Fresher
2 - 4 Hires

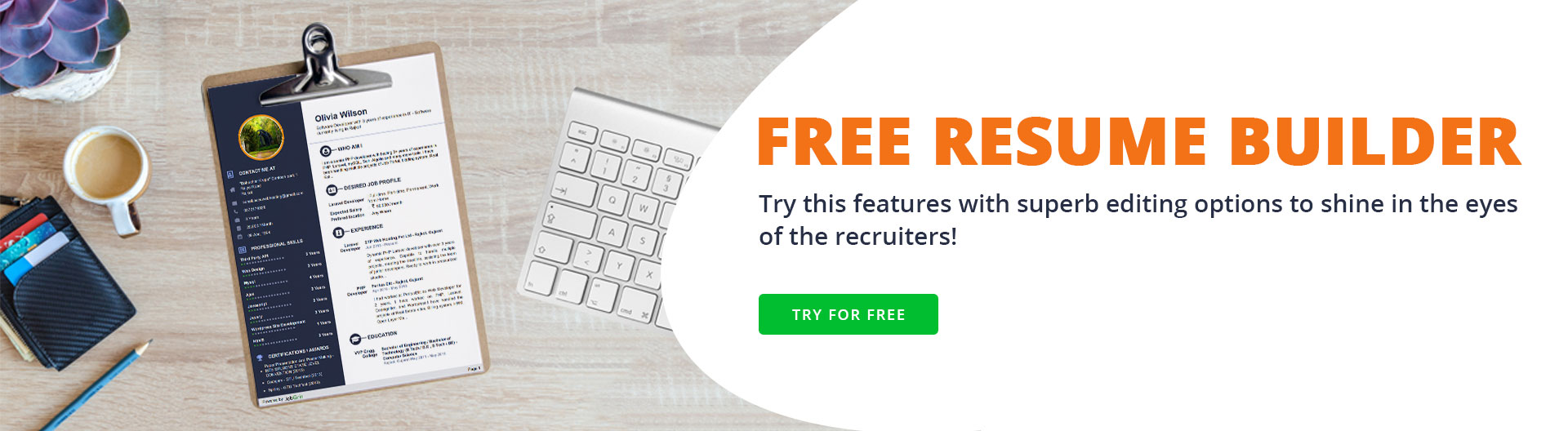
