Quality Manager Job in Zetwerk Manufacturing Businesses Pvt. Ltd.
Quality Manager
- Faridabad, Faridabad District, Haryana
- Not Disclosed
- Full-time
Company Profile and Responsibilities
Quality Manager
Responsible for leading the quality team, ensuring all quality systems, standards and processes with the global industry standards and customer requirements.
-Creating and maintaining the Company's Quality Standards; develop, implement and maintain the Company's quality documentation, such as quality procedures, reports etc.
-Design, deploy, manage Quality System - QA, Customer Complaints, RCA, Issue Management, Training, Six Sigma tools, Value Stream Mapping, etc.
-Liaise with managers and operators to ensure the smooth introduction of new products and processes and for reporting and reducing quality issues
-Liaise with other managers and staff and provide training, tools and techniques to enable others to achieve quality standards. Train & manage a team of quality control inspectors and technicians for good performance during audits.
-Inspect to ensure that products and processes comply with requirements, using established engineering techniques
-Teach the production team about quality control concerns to improve product /process excellence.
-Should Have Knowledge of 7 QC Tools, DMAIC Approach, 8D and PDCA Cycle
-Should be aware of RCA,5W1H, ISO 9001, QMS, SPC, MSA
-New development, APQP, PPAP and project management with NPI/NPD Team.
-Frame SOP s Across Processes from quality stand point
-Implementing quality protocols under the Assumed quality budget.
-Quality analysis of various raw materials (IQC) WIP, (LQC) ,FG(OQC) & PDI
-Process and quality Assurance.
-To implement statistical techniques (MSA, SPC etc).
-Develop full fledged test protocol for various categories, closely work with third party/supplier/internal stakeholders for protocol finalisation/ alignment
-Always updated to latest regulatory requirements & complying 100% to to, BIS, IS, R marking related norms
-Review customer requirements and devise plans for meeting them and timely delivery of documents
-Work with purchasing staff to establish quality requirements from external suppliers - assessment & development
-Set standards for quality as well as health and safety, communicate changes that may be required to management.
-Reduce waste and increase efficiency to ensure quality on production lines and across all departments.
Define & train quality procedures in conjunction with operating staff & establish assembly line Poka Yokes in an economical way. Ascertain redundancies in the assembly line to build resilience against rejections.
-Monitor performance by gathering relevant data and producing statistical reports to root out issues.
-Act as an external auditor and assess QMS procedures, documents and the performance of all the functions across the organization, suggest improvements and assess the effectiveness of changes made.
-Effectively communicate with customers to understand specific quality requirements and anticipate the critical audit points to be better prepared for the audit.
-Must be able to show a good practical use of measuring equipment and measuring techniques
-Spearhead competency building in areas of SPC, RCA & CAPA, QMS, Training & Development.
-Role model for QMS, Six Sigma, LEAN & Continuous Improvement body of knowledge in the organization.
-Must know implementation of ISO9001, TS16949, ISO14000, ISO45001, VDA 6.3 & APQP thoroughly.
Requirements
Experience: 8-10 Years
Education Qualification: Any Graduation from National Tier 1 or State tier 1 Institutes.
Other Skills: Good analytical and Interpersonal Skills, Attention to detail,Six Sigma Certification.
8 to 10 Years
2 - 4 Hires

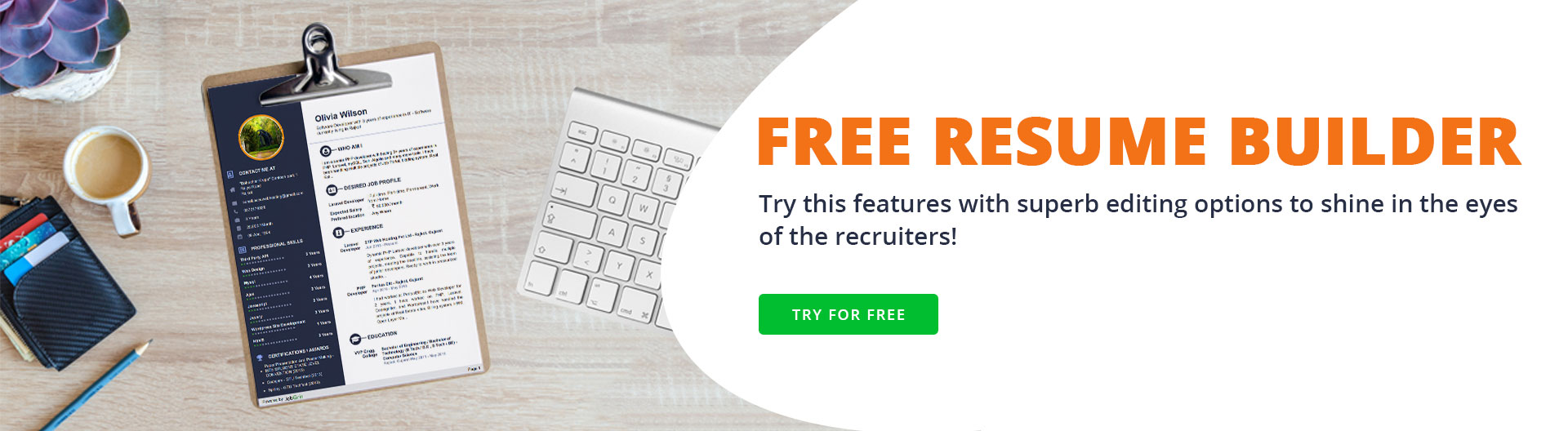
