Lead Product Engineering Development Job in Titan Company Limited
Lead Product Engineering Development
Titan Company Limited
4+ weeks ago
- Hosur, Krishnagiri, Tamil Nadu
- Not Disclosed
- Full-time
Job Summary
Role Overview The position involves leading the Product Engineering Development (PED) function at the Movement plant. The PED team is tasked with developing process routings for Movement components, identifying and implementing new manufacturing techniques, managing engineering change request trials, conducting trials for new materials and processes, establishing alternative production sources, and analyzing competitor products for process and quality insights. Additionally, the team will create action plans based on market return feedback. External and Internal Interfaces External Interfaces: Vendors (Materials, Tools, Special Process Manufacturing) Testing Laboratories Internal Interfaces: R&D (Product Design) Movement Manufacturing Shops Assembly (Internal Customers) Sourcing Material Engineering Quality Assurance Subcontracting Teams Planning Job Requirements Education: B.E. in Mechanical Engineering or Production Technology Experience: 12-15 years of relevant industrial experience Behavioral Skills: Proficient in exploring process improvements and implementing best manufacturing practices Strong research orientation towards new processes and materials for cost efficiency and smoother workflows Regular benchmarking of processes and manufacturing technologies, especially in Horology and precision component manufacturing Knowledge: Proficiency in engineering drawings and 2D/3D software Understanding of Material Science and Metallurgy Familiarity with various manufacturing processes Knowledge of analysis and simulation software Awareness of manufacturing practices such as Lean, TQM, and Six Sigma Experience in tool, die, and fixture manufacturing Expected Contributions to Processes Movement Manufacturing: Process Improvement Optimize processes, revisiting cycle and standard times to identify improvement opportunities. Develop new process routings to streamline component flow. Benchmark against similar industries for process innovations. Address process limitations and propose new methods and tooling solutions. Performance Measures: Lead time reduction and capacity optimization Improved workflow and debottlenecking Breakthrough process improvements Daily output per machine Number of new processes developed Cost of operations Movement Manufacturing: Engineering Solutions Optimize engineering processes and enhance efficiency in secondary operations (e.g., deburring, chip removal). Performance Measures: Annual reviews of processes Efficiency improvements in secondary operations Number of process enhancements Reduction in lead times and temporary labor for secondary operations Movement Manufacturing: Process Documentation and Trials Create detailed Operational Procedure Sheets for each product, covering all dimensions and critical quality checks. Document changes to products and the rationale behind them. Conduct trials to improve process quality and delivery, documenting outcomes and feedback for product upgrades. Coordinate quick prototyping for new components with the in-house Proof of Concept (POC) cell. Performance Measures: Number of Operational Procedure Sheets created Success of process trials Quantity of POC components produced from alternate sources Movement Manufacturing: Quality Assurance Conduct root-cause analysis for recurring defects based on market feedback. Track milestones for engineering change requests and design upgrades. Establish quality parameters for treatment processes and develop corresponding Standard Operating Procedures (SOPs). Create SOPs for finishing operations (Turning and Machining). Performance Measures: Completion of market reduction initiatives Documentation of engineering change requests Decrease in market returns Reduction in quality feedback from assembly processes Movement Manufacturing: Alternate Sources and Materials Benchmark competitor materials in precision industries. Identify local sources for materials to reduce import dependency. Coordinate trials for alternative materials and sources, ensuring compatibility with existing processes. Performance Measures: New sources of raw materials established Adoption of alternative materials Cost savings achieved through alternative sourcing Movement Manufacturing: Preparation for Mass Production Collaborate with R&D and tool manufacturing teams to design stamping tools and prepare for mass production. Work with manufacturing shops to design jigs, fixtures, gauges, and sub-assembly tools for new components. Incorporate feedback from manufacturing trials into product designs for mass production. Performance Measures: Development of new stamping tools for mass production Successful mass manufacturing of new components Number of new movements/components transitioned to mass production
Qualification : B.E (Mechanical Engineering / Production Technology)
Qualification : B.E (Mechanical Engineering / Production Technology)
Experience Required :
12 to 15 Years
Vacancy :
2 - 4 Hires

Similar Jobs for you
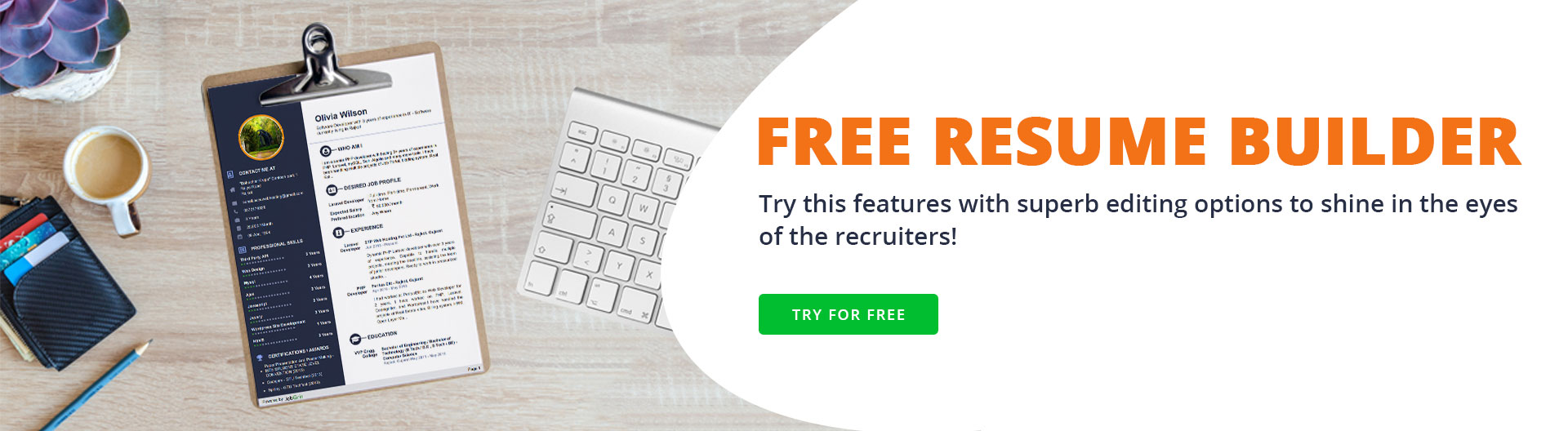

Help us improve TheIndiaJobs
Need Help? Contact us